Z czego powstają pelety drzewne - wood pellets?
Odpowiedź jest prosta z trocin i to bez dodawania jakichkolwiek lepiszczy. Z założenia czyste drewno. Do produkcji peletów drzewnych wykorzystuje się surowiec odpadowy z tartaków, stolarni, zakładów drzewnych. Najłatwiejsze jest wykorzystanie czystych, suchych, trocin.
Od tego zaczyna zwykle większość zakładów. Jednak w miarę wzrostu produkcji i konkurencji na rynku zmuszone są do rozdrabniania suchych odpadów drewna, suszenia mokrych trocin i rozdrobnionych odpadów. Coraz częściej dodatkowym źródłem surowca stają się zrębki leśne.
Surowiec wykorzystywany do produkcji peletów nie może zawierać żadnych zanieczyszczeń chemicznych lub mineralnych. Takich np. jak piasek. To właśnie największa zmora peleciarzy. Sposób pozyskiwania drewna w lesie, ciągnięcie pni po ziemi, prowadzi do zabrudzenia kory. Jest w niej sporo piasku, a piasek zwiększa ilość popiołu w peletach, szlakuje popiół oraz powoduje zużywanie się części metalowych w podajnikach. Materiałem do produkcji peletów może być każdy rodzaj drewna, pod warunkiem starannego dobrania matryc granulacyjnych. Wbrew potocznym skojarzeniom nieznacznie bardziej kaloryczne są pelety z drewna iglastego.
Wielkość produkcji a technologia
Produkcja peletów jest najłatwiejsza wówczas jeśli dysponujemy własnym surowcem i do tego najlepiej suchym. Jeśli ktoś ma około 1 metra takich trocin na godzinę, to może postawić mały granulator z młynkiem i produkować około 150 kg peletów na godzinę. Mini granulatory (do kilkuset kilogramów na godzinę) są w przypadku małej ilości surowca najlepszym rozwiązaniem. Zazwyczaj jest to zespół urządzeń (młyn, granulator, chłodnica) połączonych w całość. Nawet tona w przeciągu 6-ciu godzin da w skali miesiąca niezły przychód. Będzie to bardzo zyskowne przedsięwzięcie pod warunkiem niewielkich nakładów i automatycznej produkcji opartej na gromadzonych w silosie, poprodukcyjnych trocinach. Takie rozwiązanie pozwala na ominięcie szeregu inwestycji związanych z wytworzeniem i przygotowaniem surowca.
Jeśli jednak chcemy profesjonalnie produkować pelety na dużą skalę trudno oprzeć ją na odpadach drzewnych z jednego zakładu. Niestety w Polsce w tak komfortowej sytuacji jest jedynie kilkanaście wielkich zakładów drzewnych. Do tego tylko nieliczne, jak np Barlinek, podjęły wyzwanie. Podstawową sprawą jest wielkość produkcji. Największe profesjonalne peleciarnie wytwarzają kilkadziesiąt ton na godzinę, przeszło 100 tysięcy ton peletów rocznie. Potrzeba do tego przeszło 600 tys. metrów trocin rocznie. W Polsce jeszcze takich zakładów nie ma. Największe produkują jedynie około 10 ton na godzinę, kilkadziesiąt tysięcy ton rocznie. Lecz produkcja peletów jest jedną z najszybciej się rozwijających branż.
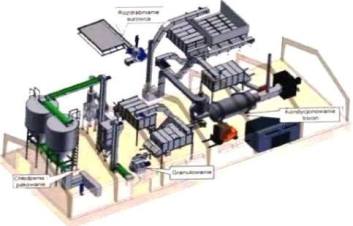 |
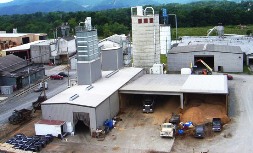 |
Apetyt rośnie w miarę jedzenia, jednak skala problemów, między innymi technicznych, rośnie razem z nim. Proponuję przyjrzeć się niektórym i przeanalizować różne sposoby ich rozwiązania. Przedstawione poniżej różne propozycje proszę traktować jako przykłady różnych, często alternatywnych, rozwiązań. Projektowanie lub rozbudowanie własnej linii do produkcji peletów wymaga każdorazowo dokonywania wielu wyborów, dla których poniższa analiza może być co najwyżej źródłem inspiracji.
PO PIERWSZE: DOSTAWA TROCIN I ZRĘBKI
Najważniejszą chyba sprawą w biznesie wood pellets jest odpowiednia lokalizacja zakładu. To właśnie ona w dłuższym okresie decyduje o sukcesie czy porażce o czym niestety niektórzy się boleśnie przekonali. Hale i technologie stawia się raz, natomiast trociny przywozi się codziennie. Powinny być one osiągalne w jak najbliższej odległości od zakładu i w miarę przyzwoitej cenie. Żeby zrobić tonę peletów trzeba średnio przywieźć 6 metrów sześciennych trocin. W przypadku wiórów po heblarce może to i być 10 metrów przestrzennych. Wydajność jednego granulatora to przedział od 0,6 do 4 ton na godzinę. W niektórych zakładach pracuje ich kilka. Średnio zawartość 35 metrowego kontenera znika w przeciągu 4 godzin. Szczęściarze zwożą trociny w promieniu 150 kilometrów. Skala zaopatrzenia to poważny problem w zakładach produkujących pelety. Trzeba utrzymać ciągłość produkcji i pełne obłożenie maszyn. To spore przedsięwzięcie logistyczne. Wymaga ze względu na ciągłość dostaw i ekonomię własnego taboru, bądź długoterminowych umów na dostawę surowca. Im dalej ruszamy po trociny tym ich więcej musimy załadować. Największe zestawy pozwalają na załadunek 100 metrów sześciennych. Często wyposażone są w ruchomą podłogę ułatwiającą rozładunek.
Załadunek takich zestawów wymaga specjalistycznego sprzętu. Wysokie burty oraz konieczność bezpośredniego ładowania sprawdza się w dużych tartakach. Często, jednak, szczególnie jeśłi chodzi o suche trociny, silosy mają małą objętość i trzeba je wielokrotnie opróżniać. Wówczas bardziej praktyczne okazują się kontenery do tzw. hakowców. Standard to pojemność 38 metrów sześciennych, plandekowane u góry. Współczesne rozwiązania tworzą z kontenerów bardzo uniwersalne narzędzia. Za pomocą wysuwanych szyn przeładowywać je można samodzielnie na platformy kolejowe. Kontenery można pozostawić wymiennie do napełnienia u klienta. Zestawione ułatwiają załadunek. Pojawiają się wersje z hydrauliczną ścianą wstępnego zagniatania, zwiększające tonaż o 20%.
W przeciętnym zakładzie produkcji peletów dwa zestawy tirowe, zabierające po dwa zsuwane kontenery, muszą non stop zwozić towar. Liczy się czas i precyzja rozładunku. Nie można dopuścić do powielania pracy. Towar musi zostać rozładowany dalej w systemie automatycznym. System kontenrowy wymaga najczęściej użytkowania kilkudziesięciu kontenerów. Rozstawiane we współpracujących zakładach drzewnych zabezpieczają płynność produkcji.
W przypadku suchych trocin rozładunek musi odbywać się pod dachem. Drewno jest materiałem higroskopijnym, równie łatwo oddaje jak i pobiera wilgoć z powietrza. Trociny powinny być magazynowane w suchych halach lub olbrzymich betonowych silosach. W zasadzie temperatura zimą nie powinna w nich spadać poniżej 10 stopni. Hydraulicznie poruszana podłoga pozwala na automatyczne pobieranie surowca. Pomocnicze mogą być systemy suwnicowe lub sprzęt mobilny ładujący trociny do różnorodnych systemów transportowych.
PO DRUGIE: WSTĘPNE ROZDRABNIANIE DREWNA ZRĘBKI I TROCIN
W odróżnieniu od brykietów, pelety wymagają starannie zmielonego i odseparowanego surowca. 6-ścio mm średnica wymaga drobin poniżej 3 mm. Technologia przygotowania surowca jest tu bardziej skomplikowana. W najbardziej rozwiniętej produkcji funkcjonują aż 3 stadia rozdrabniania. Wstępne - frakcja do 50 mm, wtórne - frakcja 6-10 mm, oraz końcowe - frakcja poniżej 3 mm.
Rozdrabnianie wstępne - efekt zrębki bez kory
Najczęściej wstępne rozdrabnianie dokonywane jest poza zakładem produkującym pelety. Transport papierówki czy drewnianych klocków jest jednak z uwagi na tonaż opłacalny. Czasami bardziej opłaca sie przywieźć materiał i na miejscu go przerobić na zrębki. Warunek materiał musi być okorowany. Celem wstępnego rozdrabniania jest doprowadzenie surowca do tak drobnej frakcji by dał się wysuszyć. To w dużym stopniu zależy od rodzaju posiadanej suszarni. Niektóre wymagają zbyt drobnej frakcji. Wówczas przyjmuje się odmienną strategie rozdrabniania do większych frakcji określonych wymogami rozdrabniarek wtórnych, najczęściej maksymalna wielkość to około 50mm.
Profesjonalnych urządzeń do wstępnego rozdrabniania jest mnóstwo Począwszy od przemysłowych rębaków, poziomych i pionowych rozdrabniarek, młynow i kruszarek. Wykorzystuje się różne techniki.
Ze względu na zróżnicowanie wielkości odpadów z drewna bardzo praktycznymi urządzeniami są popularne w Stanach tzw horizontal hogs. Zwykle są to maszyny mobilne na silnikach dieslowskich, elektryczne silniki montuje sie w wersjach stacjonarnych. Wydłużona, szeroka i lejowato podwyższona część załadunkowa z taśmociągiem i hydraulicznie amortyzowanymi wałami napędowymi, pozwala zarówno wrzucać mniejsze kawałki drewna jak i całe kłody. O wyborze urządzenia decydować musi wymagana frakcja zrębek.
Rozdrabnianie wtórne - efekt trociny
Wtórne rozdrabnianie ma sens tylko wówczas gdy wymogów suszarni co do drobnej frakcji zrębki nie da się zrealizować przy jednokrotnym rozdrabnianiu. Wówczas zmuszeni jesteśmy do instalacji młynów rozdrabniających mokre zrębki do wielkości drobnych trocin. Jest to trudne zadanie któremu mogą podołać tylko specjalistyczne, wysokoobrotowe maszyny. Problem przed którym stają to konieczność zastosowania drobnych sit które w nieodpowiednim sprzęcie szybko się zapychają. Najczęściej wykorzystuje sie do tego celu specjalnie przygotowane młyny młotkowe. Minimalna wielkość oczek w sitach tu stosowanych to 12 mm. Pozwala na uzyskanie frakcji trocin w przedziale 4-9 mm.
Jest jeszcze jedna grupa urządzeń, która doskonale sobie radzi z rozdrabnianiem mokrych zrębek , to skrawarki lub wiórkarki nożowe w niemieckim messerring zerspaner. W odróżnieniu od młynów młotkowych rozdrabnianie uzyskuje się nie przez rozbijanie zrębki lecz przez jej ścinanie. Maszyny te pozwalają na bardzo dużą precyzję w ustawieniu uzyskiwanej frakcji do 3 mm i wydajność do 9 ton przerobionego surowca na godzinę.
Dzięki tym urządzeniom przekształcamy mokre zrębki w drobne trociny. Ich praca musi być poprzedzona magnetyzerami wyłapującymi części metalowe oraz przesiewaczami kamieni. Rozdrobnienie i ujednolicenie frakcji surowca pozwala na zwiększenie wydajności linii do produkcji peletów nawet do 20%, a jego oczyszczenie podnosi żywotność wszystkich elementów linii.
PO TRZECIE: CZYSZCZENIE TROCIN I ZRĘBKI
Wymagania stawiane peletom zmuszają do starannego doboru surowca. Są zakłady wytwarzające pelety z 0,3% zawartością popiołu. Znaczy to, że z jednej tony paliwa pozostanie jego jedynie 3 kg. Żeby osiągnąć taki wynik wymagany jest całkowicie czysty surowiec. Jednakże czyste, suche trociny to coraz trudniej pozyskiwany towar. Uzupełniany odpadami, zrębkami zawierać może na każdym etapie produkcji różne części metalowe lub z metali nieżelaznych takie jak np: pociski, zszywki, gwoździe, odłupane fragmenty noży tnących, pił. Zmorą są kamienie, żwir i ziemia nagarniane w czasie załadunku a także przybrudzanie trocin stałymi elementami spalin w trakcie niewłaściwego suszenia. Nawet w najlepszych trocinach znajdujemy różnego rodzaju niepalne śmieci szkło, metal, tworzywa sztuczne. Do czyszczenia trocin wykorzystuje się różne urządzenia zarówno mechaniczne jak i pneumatyczne. Występują zarówno w postaci kombajnów czyszczących jak i pojedynczych urządzeń montowanych często wielokrotnie w poszczególnych fragmentach linii technologicznej.
Magnetyzery - oczyszczanie trocin i zrębki z części metalowych i metali nieżelaznych
Wiele firm wyposaża swoje urządzenia rozdrabniające w magnetyzery. Częściej wmontowywane są w poszczególne fragmenty linii podających surowiec. Ich zadaniem jest wychwycenie wszystkich części metalowych. Skuteczność na poziomie 99%. Spotykamy tu zarówno magnetyzery stałe w postaci płyt, prętów, sit, przez które przesuwany bądź przesypywany jest materiał, jak i ruchome w postaci walców lub taśm przesuwających a najczęściej umieszczonych powyżej podajników.
Przesuwające się taśmy magnetyczne lub walce samoczynnie zrzucają przyciągnięte części metalowe poza strumieniem trocin lub zrębki.
Ferrytowe lub neodymowe magnesy nie wymagają w przeciwieństwie do elektromagnesów prądu. Minimalny pobór związany jest z napędem silników zapewniających obrót taśmy czy walca. Można je również montować w strumieniach pneumatycznych. Metale nieżelazne zostają odseparowane dzięki sile odpychania za pomocą specjalnych magnesów wytwarzających pola wirowe.
Skuteczne wychwycenie metali wydłuża żywotność wszystkich urządzeń w procesie produkcji peletów i to jest tu sprawą najważniejszą. Naturalnie zmniejsza się również, choć nieznacznie, ilość popiołu w peletach.
Przesiewacze zrębki i trocin - segregacja frakcji
Przesiewacze to bardzo wydajne urządzenia przez które warto przepuścić wszystkie przywożone trociny i zrębki. Zwiększają one wydajność linii do produkcji peletów. Zbyt duże frakcje surowca zostaną dzięki nim oddzielone i można je wtórnie rozdrobnić. Podobnie przesiany powinien być cały materiał po wstępnym rozdrabnianiu. Bogata oferta przesiewaczy zarówno stacjonarnych jak i mobilnych pozwala dopasować je do potrzeb produkcji.
Zwykle używa się przesiewaczy wibracyjnych najczęściej jednopłaszczyznowych, w przypadku niejednorodnego materiału dwupłaszczyznowych. Materiał ponadwymiarowy zsuwany jest w dół, natomiast drobniejsze frakcje przechodzą przez sita i odprowadzane są oddzielnymi podajnikami. Wielkość frakcji zapewniają odpowiednio dobrane sita metalowe taśmowe czy druciane lub ostatnio wprowadzane gumowe i tworzywowe.
Większe kawałki drewna pomieszane z trocinami i zrębkami doskonale mogą zostać oddzielone przy pomocy przesiewaczy dyskowych. Obracające się wały z dyskami przesuwają surowiec powodując jednocześnie obsypywanie sie drobin. Odpowiednie zagęszczenie pierścieni pozwala na uzyskanie bardzo drobnej podfrakcji. W poszczególnych sekcjach przesiewacza dyskowego ich gęstość może być różna co pozwala na uzyskiwanie odmiennej frakcji.
Zbrylone trociny znacznie łatwiej przesortować w przesiewaczach bębnowych wykorzystujących rotację sita do przetrząsania materiału.
Dzięki przesiewaniu trocin i zrębki drobne frakcje kierowane mogą być bezpośrednio do suszarni lub kondycjonerów. Unika się w ten sposób zbędnego obciążania młynów wtórnego rozdrabniania. Połączenie przesiewania z segregacją za pomocą strumienia powietrza pozwala na eliminację kamieni i żwiru
Pneumatyczne czyszczalnie zanieczyszczeń mineralnych z trocin i zrębki
Weliminowanie kamieni, kurzu, piasku- słowem części mineralnych wymaga zastosowania innego sposobu segregacji. Wykorzystuje on zazwyczaj różnice w ciężarze właściwym między frakcjami trocin czy zrębki a mineralnymi zanieczyszczeniami. Jednym ze sosobów jest wprawienie strumienia surowca w ruch wirowy, który doprowadza do odrzucania cięższych drobin na stronę obwodową wiru. Takim urządzeniem jest centryfuga do czyszczenia trocin i zrębki.
Innym sposobem jest odmuchiwanie powietrzem spadającego lub przesuwanego surowca. Lżejsze frakcje zostają odepchnięte lub przyciągnięte. W tego typu urządzeniach wykorzystuje się zazwyczaj kilka sposobów oczyszczania.
Urządzenia do demineralizacji zrębki i trocin mogą w istotny sposób obniżyć zawartość popiołu w peletach jednak główną ich zaletą jest zdecydowane wydłużenie żywotności wszystkich urządzeń do produkcji pellet.
PO CZWARTE: SUSZENIE TROCIN I ZRĘBKI
Przygotowanie surowca do produkcji peletów drzewnych / wood pellets /, wymaga, oprócz rozdrobnienia i oczyszczenia, jego wysuszenia do około 8 % wilgotności. Dehydratacja, czyli usuwanie wody z trocin i zrębki, najczęściej przeprowadzana jest za pomocą podgrzewania masy drzewnej, doprowadzającego do jej parowania. Głównym zadaniem tego typu suszarń jest zapewnienie warunków do maksymalnej dyfuzji usuwanej pary wodnej w całym przekroju podawanego strumienia trocin. Szybkość parowania trocin jest w pewnych przedziałach wprost proporcjonalna do temperatury i odwrotnie proporcjonalna do poziomu wilgotności ich otoczenia. Parowanie będzie narastało jeśli usuwana będzie wilgoć z powietrza wokół trocin. Lecz nie liczy się tutaj jedynie szybkość wysuszenia trocin, bardzo ważna jest ich jakość po wysuszeniu, bezpieczeństwo oraz wysokość kosztów obsługi suszarni.
Suszarnie bębnowe bezpośrednie
Tradycyjnym rozwiązaniem są suszarnie bębnowe. Najczęściej z bezpośrednim spalinowym podgrzewaniem torcin. Bębnówki to prawdziwe konie pociągowe w suszeniu biomasy. Obracający się poziomy bęben z łopatkami po wewnętrznej stronie pozwala na stałe przesypywanie podawanych trocin w kierunku do położonego z drugiej strony wentylatora. Gorące powietrze ze spalinami o temperaturze okolo 400 stopni wdmuchiwane jest w tym samym kierunku z pieca powietrznego, bezpośrednio do bębna. Strumień powietrzno-spalinowy oraz lekkie, suche trociny wyciągane są pnęumatycznie wentylatorem i odseparowane w cyklonach.
Głównym minusem bezpośrednich suszarni bębnowych jest tendencja do mineralizacji trocin. Ciemne przebarwienia trocin związane są z osadzaniem się na nich spalin ale również są efektem utleniania na skutek podawania zbyt wysokiej temperatury. Zbyt wysoka temperatura powoduje powierzchniowe utwardzanie się trocin, hamujące uwalnianie ligniny. Pelety z takiego surowca będą ciemne i mniej spoiste, pozbawione mocnego połysku. Współczesne, nowoczesne suszarnie bębnowe pozwalają na pełną kontrolę nad wszystkimi procesami mającymi wpływ na jakość i szybkość suszenia. Komputerowe symulacje pozwoliły na eliminacje błędów konstrukcyjnych. Modyfikacje idą w kierunku regulacji prędkości przesuwania trocin w poszczególnych sekcjach bębna, budowaniu bębnów wielociągowych, rozbudowie sterowania: temperaturą spalin, prędkością podawania trocin, prędkością obrotów bębna, oraz pracą wentylatorów wyciągowego i nadmuchowego.
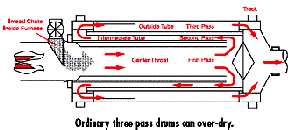 |
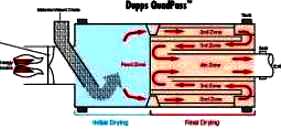 |
Zastosowanie wielociągowych rozwiązań w konstrukcji bębnów wydłuża drogę suszenia trocin, pozwala na obniżenie temperatury podawanych spalin i powietrza, różnicuje warunki suszenia. Zwiększa się dzięki temu bezpieczeństwo użytkowania i podwyższa jakość trocin. Unika się w ten sposób wielu mankamentów tradycyjnej bębnówki, między innymi zapłonów trocin.
Suszarnie bębnowe pośrednie
Zastosowanie wymienników ciepła: powietrznych lub parowych pozwala na uzyskanie w suszarniach bębnowych lepszych jakościowo trocin i zrębek. W suszarniach pośrednich nie występują problemy z mineralizacją i przegrzaniem surowca w czasie suszenia. Podawana jest niższa temperatura, różna w zależności od rodzaju użytego medium. Stosunkowo prostym rozwiązaniem, usprawniającym działanie tradycyjnych bębnówek, jest umieszczanie pomiędzy piecem a suszarnią powietrznego wymiennika ciepła. Do bębna suszarni wtłaczane jest wówczas czyste, podgrzane powietrze z wymiennika nie zawierające spalin. W zależności od rozwiązania może ono osiągać temperaturę nawet powyżej 300 stopni.
Temperaturę około 180 stopni dać może para wodna. Steam Tube Rotary Dryer to rozwiązanie bardzo popularne w Austrii krainy DIN PLUS. Wymaga ona innej konstrukcji bębna suszarni. W przypadku suszenia trocin i zrębki kilkuwarstwowa wiązka rur montowana jest obwodowo od wewnętrzenej strony bębna. Trociny przesypują się bezpośrednio pomiędzy gorącymi rurami. Istnieją również mniej popularne konstrukcje w których stanowi ona ruchomy wewnętrzny wirnik suszarni.
Para wpuszczana i odbierana jest przez centralne zawory umożliwiające rotację bębna. Rozwiązanie wymaga instalacji kotła parowego. Bębnowe suszarnie parowe to bardzo dobre rozwiązanie pozwalające na na pełna kontrolę temperatury, odzysk ciepła pary, bardzo dobrą jakość trocin. Na rynku peletów jasne posiadają wyższą cenę. Warto w związku z tym montować suszarnie z pośrednim źródłem ciepła.
W przypadku zastosowania wodnego wymiennika, dającego temperaturę około 100 stopni, wymagany jest znacznie dłuższy obieg trocin. Z punktu widzenia suszenia biomasy nie ma on uzasadnienia.
Suszarnie taśmowe trocin i zrębki
Istota rozwiązania sprowadza się do budowania jedno lub wielopoziomowych tuneli z surowcem systematycznie nasypywanym na przesuwającą się, perforowaną taśmę stalową. W wielu punktach tuneli nadmuchiwane jest na nią z góry lub z dołu gorące powietrze. Złoże może być dodatkowo wzbudzane dzięki ruchom wibracyjnym taśmy.
Główną zaletą suszarni taśmowych jest możliwość znacznego wydłużenia drogi suszenia oraz bezpośredni przedmuch gorącego powietrza przez złoże trocin czy zrębki. Pozwala to na obniżenie temperatury suszenia, dzięki czemu wzrasta jakość suszonego surowca. Wibracyjno taśmowy przesuw trocin daje możliwość połączenie suszenia z segregacją i czyszczeniem.
Strumieniowe suszarnie trocin
Im większa jest wymiana powietrza wokół poszczególnych drobin trocin tym, przy danej temperaturze, szybsze suszenie. Tę zasadę wykorzystują strumieniowe suszarnie typu Flash, wchodzące dopiero na nasz rynek. Ich działanie sprowadza się do suszenia w trakcie pneumatycznego przenoszenia trocin w strumieniu gorącego powietrza lub pary. Zmienny, silny na tyle by unieść wilgotne trociny, opływ powietrza wokół drobin prowadzi do wielostronnego parowania wody. Odpowiednio zaprojektowane rury połączone są cyklonami wytrącającymi ze strumienia trociny. Część gorącego zużytego powietrza wykorzystywana jest ponownie.
Suszarnie występują zarówno w wersji bezpośredniej - strumienia spalin , jak i pośrednio za pomocą wymienników powietrznych lub parowych. Czasami są wykorzystywane również do wstępnego suszenia w systemach mieszanych. Na szczególną uwagę zasługują rozwiązania z recyrkulacją gorącego powietrza.
Suszarnie fluidalne
Interesującą propozycją są wkraczające na rynek suszarnie fluidalane. Od strumieniowych różnią się tym, że podawany wstępnie surowiec porywany jest przez słabszy strumień powietrza dopiero wówczas, gdy spada jego ciężar wskutek odparowania wody. Wcześniej opadając na dno sita, przez które nadmuchiwane jest powietrze, tworzy tzw złoże fluidyzacyjne. Odpowiednie ciśnienie wtłaczanego powietrza unosi nieco z złoże nad powierzchnię sita. W miarę wysychania trocin zaczynają one cyrkulować, proces przypomina nieco wrzenie wody. Wysuszone drobiny stopniowo stają się lżejsze dzięki czemu zostają ostatecznie porwane przez gorące powietrze i oddzielone od niego w cyklonach. Suszarnie te występują zarówno w wersji poziomej przypominającej trochę suszarnie taśmowe jak i w wersji kolumnowej.
Suszarnie fluidalne czy fluidyzacyjne pozwalają na szybkie i wydajne odparowanie wody z trocin, Różne warianty podawania powietrza np. pulsacyjne, fontannowe wraz z różnym sposobem wibracji sita mogą dodatkowo wspomagać proces fluidyzacji. Zaletą jest naturalne w tym systemie czyszczenie surowca z części mineralnych takich jak kamienie, które opadają na dno sita i mogą być automatycznie odseparowane. Podobnie większe frakcje zrębki czy kawałki drewna mogą być odprowadzane do spalania lub rozdrabniania. Część zużytego gorącego powietrza można ponownie użyć do suszenia.
Technik suszenia trocin jest bardzo wiele. W ostatnim czasie dynamicznie się rozwijają. Eksperymentuje się przy zastosowaniu do suszenia trocin między innymi pomp próżniowych czy mikrofali. Niezależnie jednak od techniki suszenia najważniejsze zawsze pozostaje: wysokość kosztów suszenia, realna efektywność suszarni w najtrudniejszych warunkach, jakość wysuszonego produktu i bezpieczeństwo pracy. Każdą z technik rozwinąć można kierując się tymi kryteriami.
PO PIĄTE : KOŃCOWA OBRÓBKA TROCIN - EFEKT MIAŁ DRZEWNY
Rozdrabnianie końcowe
Po wysuszeniu trociny muszą zostać ostatecznie zmielone. Dotyczy to również trocin przywiezionych jako suche, naturalnie po wcześniejszym ich przesianiu i wyczyszczeniu. Aby uzyskać zwarte i twarde pelety 6-ścio milimetrowe frakcja miału nie powinna przekraczać 3 mm. Najczęściej jest to około 1,2 mm. Drobny miał nie tylko poprawia jakość peletów ale i pozwala granulatorom na osiągnięcie większej wydajności. Tu już zdecydowanie dominują młyny młotkowe z drobnymi sitami. Zbyt drobna frakcja, jak pył drzewny, stwarza również problemy przy granulowaniu.
Młyny najczęściej wyposażone są w sita o oczkach 5 mm. Dodatkowo posiadają w części wsypowej magnetyzery wyłapujące drobiny metali. Trociny rozbijane są młotami i rozcierane o sita. W efekcie powstaje miazga drzewna nadająca się do granulowania.
Kondycjonowanie miazgi drzewnej
Parować czy nie parować miazgę drzewną? Zdania są podzielone. Wydaje się, że sensowność parowania zależy od sposobu suszenia trocin, od rodzaju trocin oraz od wymogów rynku. Miazga potraktowana tzw suchą parą o temperaturze 180 stopni ma "uwolnioną" ligninę, stanowiącą naturalne lepiszcze. Para nie tylko aktywizuje ligninę miazgi ale także otacza ją filtrem zmniejszającym tarcie w trakcie granulowania. Można się o tym łatwo przekonać granulując twarde i "suche" gatunki trocin np. bukowych. Bez dodania pary granulator będzie z powodu nadmiernych oporów aż "podskakiwał". Pelety z miazgi parowanej mają szklistą powłokę i są mniej kruche. Naturalnie dozowanie suchej pary musi być bardzo precyzyjne, nadmiar da efekt odwrotny. Przeciwnicy parowania często dodają do 2% mąki do trocin. Być może ułatwia ona granulowanie, lecz wywołuje szlakowanie się popiołu ze względu na zawartość pierwiastków alkalicznych takich jak wapno czy potas. Zanim dosypiecie tzw. ulepszaczy warto pomyśleć na reklamacjami. Dobrze dozowana i odpowiednia sucha para jest najlepszym ulepszaczem.
Urządzenia w których paruje się miazgę i jednocześnie ją miesza to kondycjonery. Muszą one umożliwiać równomierne rozprowadzenie pary i pozwalać na jej precyzyjne dozowanie. Niektóre granulatory są już w nie wyposażone, częściej trzeba je wkomponowywać w linię.
Kondycjonery pozwalają na regulację ilości dostarczanej pary i jej rozprowadzenie. Para dostarczana musi być z generatora pary. Najczęściej spotykane są u nas generatory gazowe lub olejowe, ze względu na wygodę użytkowania. Równie skuteczne i w peleciarniach zdecydowanie tańsze w eksploatacji są generatory z palnikiem na pelety.
Suszenie trocin w strumieniu pary pozwala na wyeliminowanie kondycjonerów.
PO SZÓSTE GRANULOWANIE TROCIN (MIAZGI DRZEWNEJ)
Tylko odpowiednio przygotowany surowiec drzewny pozwala na skuteczne zagęszczenie w granulatorach. Naturalnie, najprostsze będzie to w przypadku zagęszczania suchych, czystych trocin bezpośrednio z produkcji. Wówczas odpada wiele etapów wstępnego przygotowania materiału. Bezpośrednio po zmieleniu poddać je można zagęszczaniu w procesie granulowania.
Granulator to serce całego procesu produkowania peletu. Od jego pracy zależy bezpośrednio sukces całego przedsięwzięcia. Przyjrzyjmy się zatem różnym rozwiązaniom.
Granulowanie pod lupą
Wytwarzanie peletów to proces wielokrotnego wyciskania miazgi drzewnej przez specjalnie ukształtowane otwory w grubej metalowej matrycy.
Bezpośrednia jakość peletów zależy od wielu czynników związanych z mechaniką docisku, cechami matrycy z otworami, sposobem podawania miazgi drzewnej i od właściwości samej miazgi. Liczy się siła docisku rolek do matrycy, ich wzajemna prędkość decydująca o grubości wciskanej warstwy, ukształtowanie ryfli w rolkach dociskających, wysokość i średnica otworów ( grubość matrycy), ukształtowanie lei otworów od wewnętrznej i zewnętrznej strony matrycy, szybkość i równomierność podawania i rozprowadzania miazgi drzewnej na całej szerokości matrycy.
Charakterystyka matrycy musi być dopasowana do rodzaju drewna. W trakcie pracy powstają różnorodne zależności i zmiana nawet jednej cech może doprowadzić do nieoczekiwanych konsekwencji.
Typy granulatorów
To kształt matrycy i system dociskania decyduje w zasadzie o typie granulatora. Na rynku granulatorów drzewnych funkcjonują dwie odmiany matryc płaskie (koliste) oraz przestrzenne (pierścieniowe). Wśród tych pierwszych nieodmiennie króluje niemiecka firma Kahl, znany producent młynów.
Granulatory z matrycą pierścieniową najczęściej pracują w układzie wyciskania odśrodkowego za pomocą jednej, dwóch lub trzech obrotowych rolek, dociskających miazgę drzewną do wewnętrznej powierzchni matrycy. Pelety wyciskane są na zewnątrz matrycy i tam ścinane na odpowiednią długość. To najbardziej popularna odmiana granulatorów do peletów drzewnych, produkowana przez kilkandziesiąt firm, w tym dwie polskie. Prym wiedzie tu amerykańska CPM (poniżej schemat jej granulatora) i europejska Andritz-Matador. Ta ostatnia jest jedną z nielicznych firm, która zaprojektowała od początku granulator specjalnie do przerobu trocin (miazgi drzewnej), najczęściej spotykamy wzmocnione adaptacje granulatorów paszowych. Wydajność tego typu urządzeń, przy danym surowcu, zależy bezpośrednio od roboczej powierzchni matrycy i jest pochodną jej obwodu i szerokości. Zależy ona również od powierzchni docisku rolek do matrycy a ta wyznaczona jest przez szerokość rolek i ich liczbę. Dalej o wydajności decyduje już wzajemna prędkość matrycy i rolek dociskających oraz grubość prasowanej warstwy surowca ograniczana przez średnicę rolek i siłę ich docisku.
Nowością w technologii wood pellets są granulatory z prasującymi matrycami, oparte na koncepcji wyciskania dośrodkowego. Technologia ta popularna jest od dawna w przemyśle farmaceutycznym. Pozbawione zespołu rolek dociskających osiągają wydajność nawet do 10 ton na godzinę.
Ta ostatnia rodzina granulatorów rokuje spore nadzieje, szczególnie w budowie granulatorów o dużej wydajności. Szerokość matrycy nie jest w nich bowiem ograniczana oporami jakimi obciążane są łożyska rolek dociskających. Tutaj nacierają na siebie jedynie dwie matryce, które mogą być znacznie szersze. Już dzięki temu, że zawsze pracują dwie, podwojona jest ich powierzchnia robocza. W przeciwieństwie do granulatorów z matrycą odśrodkową niesprasowana miazga drzewna spada i trzeba ją pneumatycznie doprowadzać ponownie do zbiornika.
autor Lech Kowalewski
zobacz także:
Pelety drzewne (wood pellets) wymagania rynku a normy.
Polish pellets - sezon za nami, nadchodzą ciężkie czasy.
Zmiany na polskim rynku brykietów
Pellets Expo 2007 na jałowym biegu